What is CNC Machining?
CNC (Computer Numerical Control) uses a computer controlled machine tool to remove material from a block of raw material or a pre-existing part, which can help producers achieve fast and accurate part creation at high efficiency and low cost. The advantages of CNC machining make it the preferred manufacturing method for several industries.
CNC Machining With HYLUO
At Hyluo, we offer comprehensive precision CNC machining services that enable you to obtain high-quality and accurate parts in a time-efficient and cost-effective manner.
3 axis, 4, and 5-axis CNC machining
Milling, Turning, Surface treatment
From prototype to high-volume
ISO 9001 : 2015 and IATF Certified.
Our CNC Services
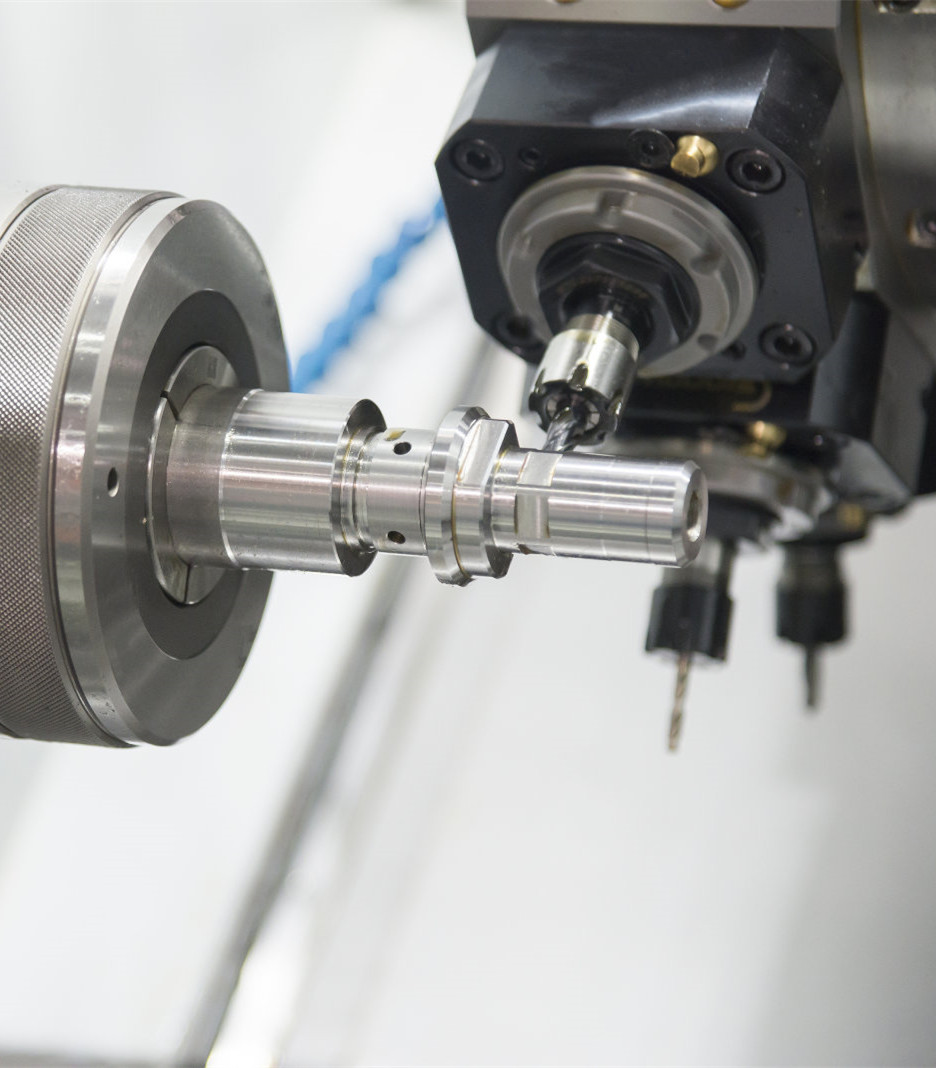
CNC Turning
Stardard and live tooling capabilities for all types of cylindrical shapes, such as flanges and shafts. Learn more about how we can support you.
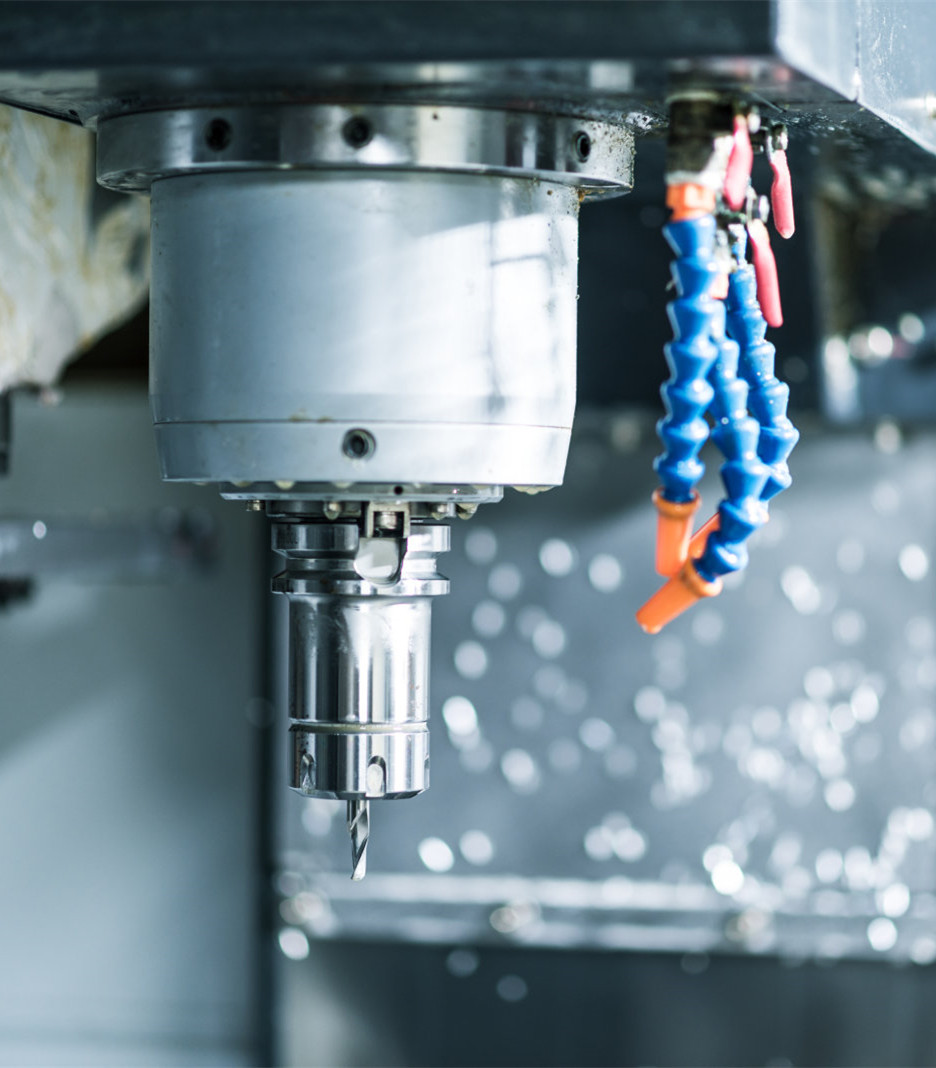
CNC Milling
CNC Milling makes compex geometries for various industries. with our CNC 3-axis, 4-axis and full 5-axis machining services, start your new part now.
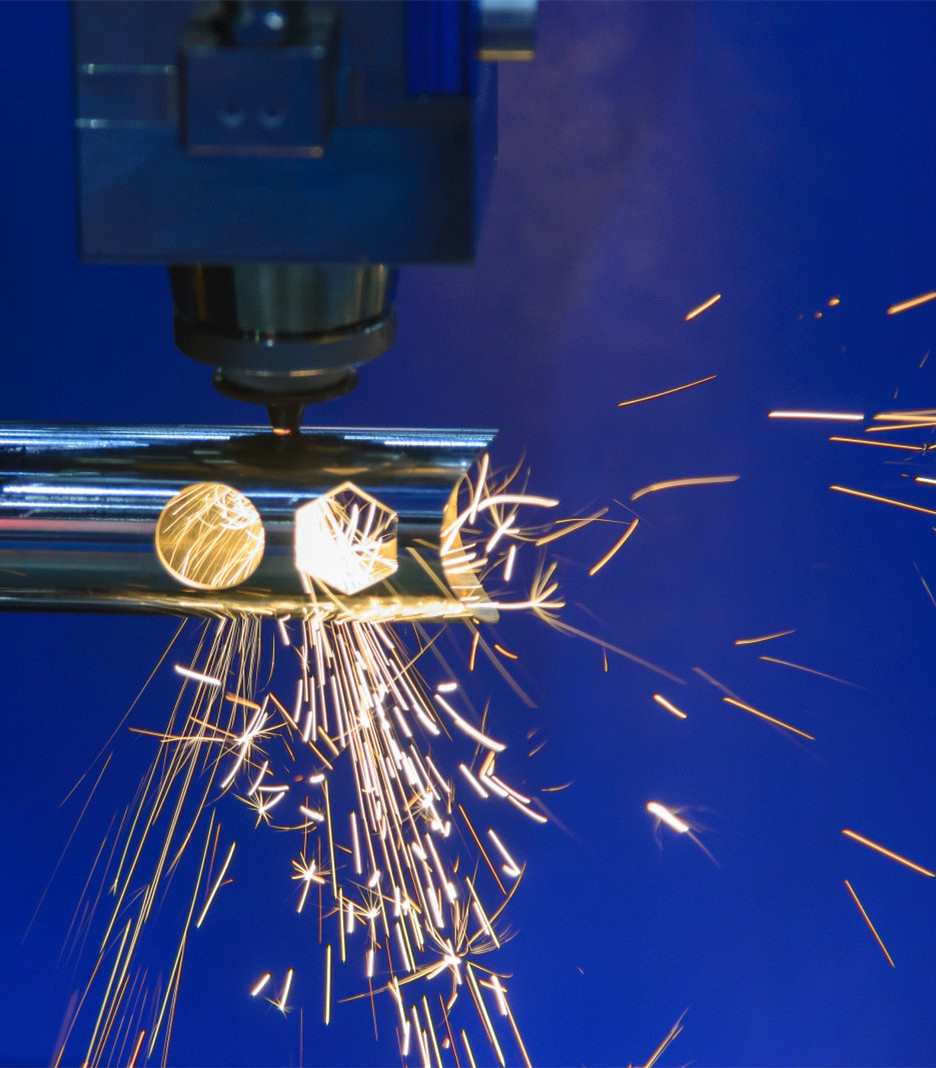
Secondary Services
As a full-service source for machined components, we provides necessary secondary operations such as assembly, surface finishing, heat treatment, etc.
Why Choose HY CNC Machining
Purchasing Steps
1 : Send your CAD files or samples to us for a quick quote;
2 : Configure your part specifications and select a lead time;
3 : We produce parts strictly according to your requirement;
4 : You get the parts in good condition on time by air or sea;
Materials for CNC Machining
Surface Finishes for CNC Machining
Servious surface finishings for machined parts are available, Below the main surface treatments from Hyluo:
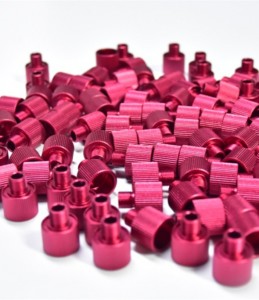
Anodizing
Anodizing is most commonly used to protect aluminum alloys, improve corrosion resistance and adhesion, increase oxidation color.
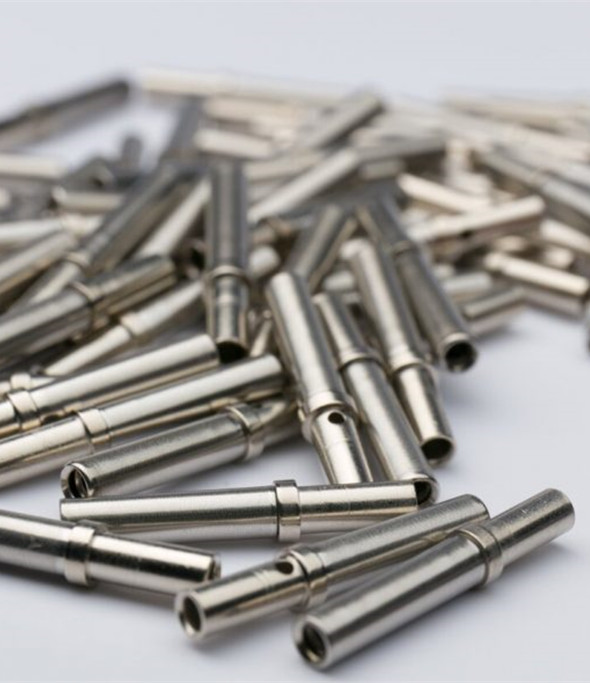
Nickel Plating
Nickel plating is to plate a layer of nickel on the surface of parts, can improve corrosion resistance, increase gloss and beauty.
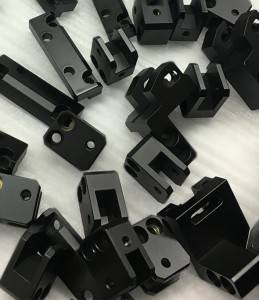
Black Oxide
Black oxide is a conversion coating which is used on steel, stainless steel and copper. It can improve the corrosion resistance of parts.
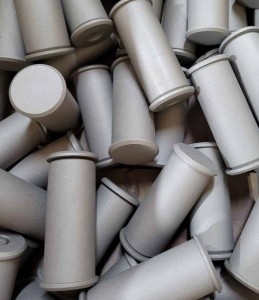
Sandblasting
Sandblasting is to use the impact of high-speed sand flow to clean and roughen the surface of parts. Different roughness can be selected.
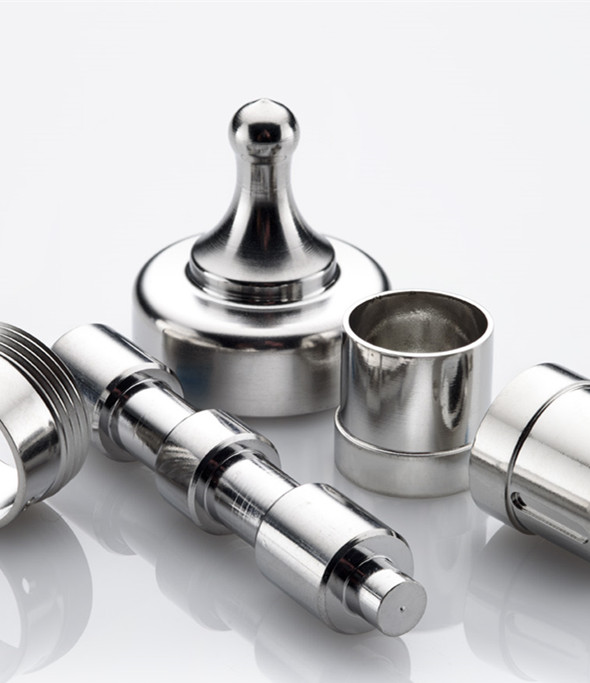
Electropolishing
Electropolishing dissolves the fine burrs on the surface of parts through DC ionization reaction, making the parts bright and clean.
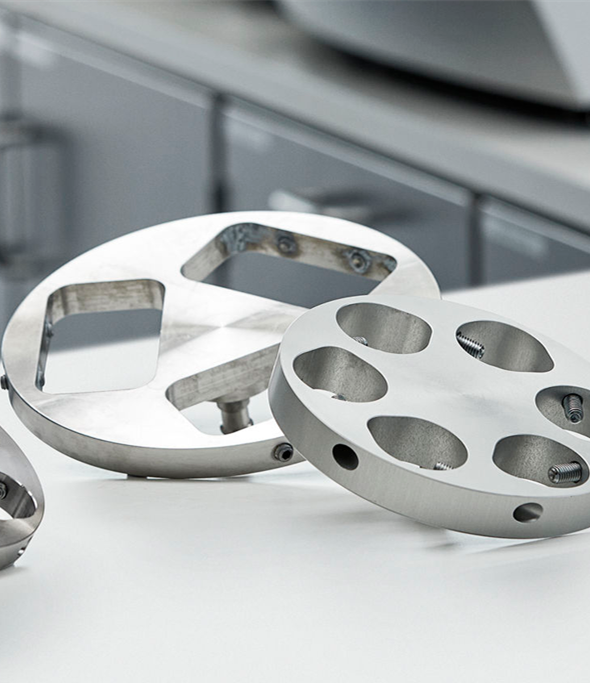
Polishing
Polishing can make the surface of parts smooth and bright. It can prevent corrosion, remove oxidation and improve service life.
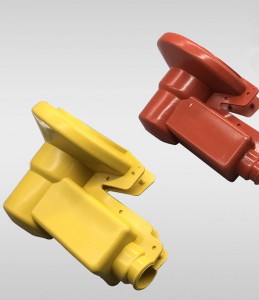
Spray Painting
Spray painting is to spray coating material (paint, ink, varnish, etc.) through the air onto the surface of parts, it can make parts colorful.
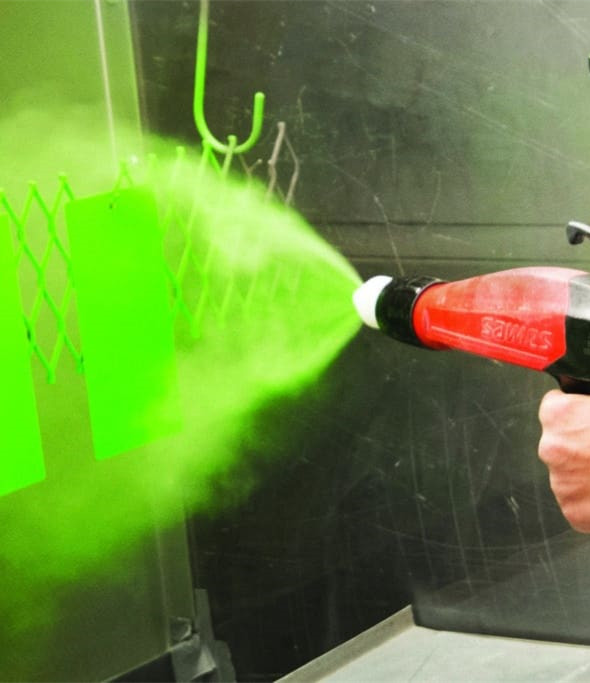
Powder Coating
After powder coating on the surface of parts, it can improve the wear resistance, corrosion resistance and anti-aging of parts.
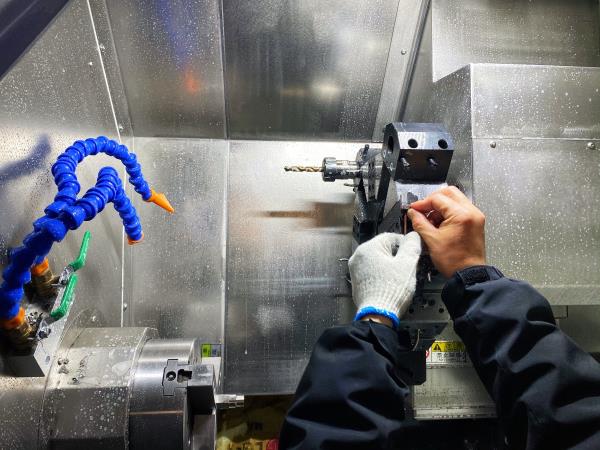
Advantages of CNC machining
CNC machining is an efficient and new type of automatic machining method, which has a wide range of application prospects. It has the following advantages:
The adaptability and flexibility of machining parts
High precision, the accuracy can reach 0.005~0.1mm.
High production efficiency and stable quality.
Low labor intensity and good working conditions
Conducive to modern production and management.
CNC machining applications
CNC machining has proven to be an outstanding method for manufacturing complex-shaped and high-precision parts that require frequent product changes and short production cycles. It is widely utilized in various industries:
Airplane,
Cars,
Shipbuilding,
Power equipment,
National Defense Military Industry, etc.
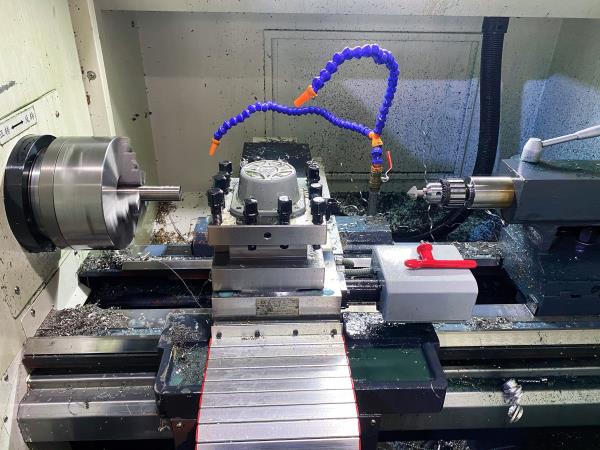
CNC machining FAQs
CNC machining, which stands for Computer Numerical Control machining, is a manufacturing process that uses pre-programmed computer software to control the movements of machinery and tools. CNC machines use a range of cutting tools to remove material from a workpiece, creating a final product with a precise shape and dimensions.
In CNC machining, the design for the part is first created using computer-aided design (CAD) software. The design is then translated into a set of instructions that the CNC machine can understand and execute. These instructions control the movement of the cutting tools along multiple axes, allowing for complex shapes and geometries to be machined with high precision and accuracy.
CNC machining can be used to produce parts from a variety of materials, including metals, plastics, and composites. It is commonly used in industries such as aerospace, automotive, medical, and electronics, where precision and consistency are essential.
Advances in CNC technology have led to the development of various types of CNC machines, including milling machines, lathes, routers, and grinders. Each type of machine is designed for specific machining applications and can produce a wide range of parts with high accuracy and repeatability.
The cost of CNC machining can vary depending on several factors such as the complexity of the part, the quantity of parts needed, the material used, the type of CNC machine required, and the level of finishing required.
Part complexity: The more complex the part, the more time and machining operations required to produce it, which will increase the cost.
Material: The cost of the material used will depend on the type and quantity needed. Certain materials such as exotic metals or high-performance plastics may be more expensive.
Quantity: The quantity of parts needed can impact the cost of CNC machining. In general, the cost per unit will decrease as the quantity of parts ordered increases due to economies of scale.
Finishing: Additional finishing operations such as polishing, painting, or anodizing will increase the overall cost of CNC machining.
Machine type: Different types of CNC machines have different capabilities and are used for different applications. The cost of machining will depend on the type of machine required to produce the part.
As a result, it's difficult to give a precise estimate of the cost of CNC machining without specific details about the project. To get an accurate estimate for your project, Contact Hyluo's CNC sepecialist today with specific details.
As a professional Chinese CNC machining factory, we take great pride in delivering machined parts with tight tolerances to our customers. Our capabilities for tolerances are as follows:
We can achieve tolerances as tight as +/- 0.005mm for most materials and geometries, depending on the specific part requirements. However, we also recognize that each part is unique and may have different tolerance requirements. Therefore, we work closely with our customers to understand their specific needs and provide the most appropriate solutions to achieve their desired tolerances.
To ensure that our parts meet the required tolerances, we use state-of-the-art CNC machines, which are regularly maintained and calibrated. Additionally, we have a strict quality control process in place that includes inspection at various stages of production to ensure that the parts meet the required tolerances.
At our factory, we are committed to delivering high-quality machined parts that meet the strictest specifications and requirements of our customers. If you have any specific tolerance requirements for your project, please feel free to contact us, and our team will work closely with you to provide the best solution for your needs.
Our production lead time can vary depending on the complexity of the parts, the quantity of parts needed, the material used, and the level of finishing required. However, we strive to provide our customers with the fastest and most efficient lead times possible without compromising the quality of the final product.
In general, our production lead time for CNC machining parts is typically around 2-4 weeks, depending on the specific project requirements. However, for simpler parts or smaller quantities, we can often produce parts much faster. On the other hand, more complex parts or larger quantities may require longer lead times.
We understand that timely delivery is critical to our customers' success, and we work hard to ensure that our production schedules are optimized for the most efficient turnaround times. Our team is dedicated to providing clear communication throughout the production process to keep our customers informed of their project's progress and delivery dates.
If you have any specific requirements or deadlines for your project, please feel free to contact us, and we will work closely with you to provide the best possible production lead time for your needs.
We understand that delivering high-quality machined parts is critical to our customers' success. Therefore, we have implemented a comprehensive quality control system that ensures all parts meet the required specifications and tolerances.
1. Inspection at multiple stages: We conduct quality inspections at multiple stages of the production process, including incoming material inspection, in-process inspection, and final inspection. This helps us identify any potential issues early on and ensure that the final product meets the required specifications.
2. Advanced measurement tools: We use advanced measurement tools, such as coordinate measuring machines (CMMs) and optical measuring machines, to accurately measure the dimensions of the parts and ensure that they meet the required tolerances.
3. Skilled workforce: Our team of skilled machinists and quality control technicians have extensive experience in CNC machining and are trained to identify and address any quality issues that may arise during production.
4. Quality control standards: We adhere to strict quality control standards, such as ISO 9001 and AS9100, to ensure that our processes and procedures meet international quality standards.
5. Continuous improvement: We are committed to continuous improvement and regularly review our processes and procedures to identify areas for improvement and implement corrective actions.
At our factory, we are dedicated to delivering high-quality machined parts that meet our customers' exact specifications and requirements. If you have any specific quality control requirements for your project, please feel free to contact us, and our team will work closely with you to provide the best possible quality control solution for your needs.
CNC (Computer Numerical Control) machining is a highly precise manufacturing process that uses automated machines to cut, drill, and shape materials into finished products. Some of the advantages of CNC machining include:
2. Speed: CNC machines can produce parts much faster than manual machining methods, reducing production time and increasing output.
3. Versatility: CNC machines can work with a wide variety of materials, including metals, plastics, composites, and more.
4. Efficiency: CNC machines are highly automated, requiring minimal human intervention, which reduces labor costs and increases productivity.
5. Flexibility: CNC machines can be programmed to produce a wide range of complex parts with intricate shapes and designs, making them ideal for prototyping and low-volume production runs.
6. Consistency: CNC machines can produce identical parts with consistent quality, ensuring that every part meets the same high standard.
7. Cost-effective: CNC machining can be cost-effective for both high-volume production runs and low-volume custom orders, making it a versatile and economical manufacturing process.
Overall, CNC machining offers many advantages over traditional manual machining methods, making it a popular choice for industries that require precision, speed, and efficiency.