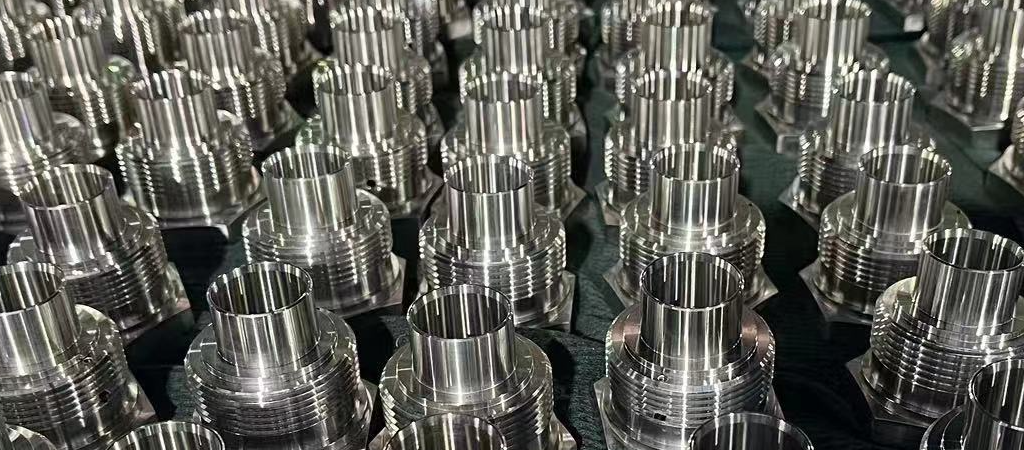
The machining center is a typical mechanical processing equipment integrating high and new technologies. According to statistics, machining centers are currently one of the most widely used CNC machine tools in the manufacturing industry. Its development represents the level of design and manufacturing in a country. Machining centers have become the mainstream direction of the development of modern machine tools and are widely used in the machinery manufacturing industry. Compared with ordinary CNC machine tools, they have the following outstanding characteristics.
1. Process concentration
The machining center is equipped with a tool magazine and can automatically change tools, which can realize multi-process processing of workpieces. After the workpiece is clamped once, the CNC system can control the machine tool to automatically select and replace tools according to different processes, and adjust the spindle speed and feed. Quantity, motion trajectory. Modern machining centers enable the workpiece to achieve continuous, efficient, and high-precision processing of multiple surfaces, multiple features, and multiple stations after one clamping, that is, process concentration. This is the most outstanding feature of the machining center.
2. Strong adaptability to processing objects
The machining center can realize flexible production. The flexibility of production is not only reflected in the rapid response to special requirements, but also can quickly realize mass production and improve market competitiveness.
3. High processing precision
The machining center, like other CNC machine tools, has the characteristics of high machining accuracy. Moreover, the machining center avoids multiple clamping due to the centralized processing process, so the machining accuracy is higher and the machining quality is more stable.
4. High processing efficiency
The time required for parts processing includes maneuvering time and auxiliary time. The machining center is equipped with a tool magazine and an automatic tool changer. It can complete multiple processes on one machine tool, thereby reducing the time for workpiece clamping, measurement and machine tool adjustment, and reducing the turnover, transportation and storage time of semi-finished workpieces, making it easier to The cutting utilization rate (ratio of cutting time and starting time) of CNC machine tools is 3 to 4 times higher than that of ordinary machine tools, reaching more than 80%.
5. Reduce the labor intensity of operators
The processing of parts by the machining center is automatically completed according to a pre-programmed program. In addition to loading and unloading parts, performing intermediate measurements of key processes and observing the operation of the machine tool, the operator does not need to perform heavy repetitive manual operations, labor intensity and tension. can be greatly alleviated, and working conditions have also been greatly improved.
6. High economic benefits
When using a machining center to process parts, the equipment cost allocated to each part is more expensive, but in the case of single-piece, small-batch production, many other costs can be saved, so good economic benefits can be obtained. For example, adjustment, machining and inspection time can be shortened after the part is installed on the machine tool, reducing direct production expenses. In addition, because the machining center processes parts without the need to make other fixtures, hardware investment is reduced, and because the processing quality of the machining center is stable, the scrap rate is reduced, so the production cost is further reduced.
7. Conducive to the modernization of production management
Using a machining center to process parts can accurately calculate the processing hours of parts, and effectively simplify the management of fixtures and semi-finished products. These features are conducive to modernizing production management. Currently, many large-scale CAD/CAM integrated software have developed production management modules to realize computer-aided production management. Although the process collection processing method of the machining center has its unique advantages, it also brings many problems, which are listed below.
1) After rough machining, the workpiece enters the finishing stage directly. The temperature rise of the workpiece has no time to recover, and the size changes after cooling, which affects the accuracy of the workpiece.
2) The workpiece is directly processed from the blank into the finished product. In one clamping, the amount of metal removal is large, the geometric shape changes greatly, and there is no process of stress release. After a period of processing, the internal stress is released, causing the workpiece to deform.
3) Cutting without chips. The accumulation and entanglement of chips will affect the smooth progress of processing and the surface quality of parts, and even cause damage to the tool and scrap the workpiece.
4) The fixture for clamping parts must meet the requirements of being able to withstand large cutting forces during rough machining and accurately positioning during finishing, and the clamping deformation of the parts must be small.