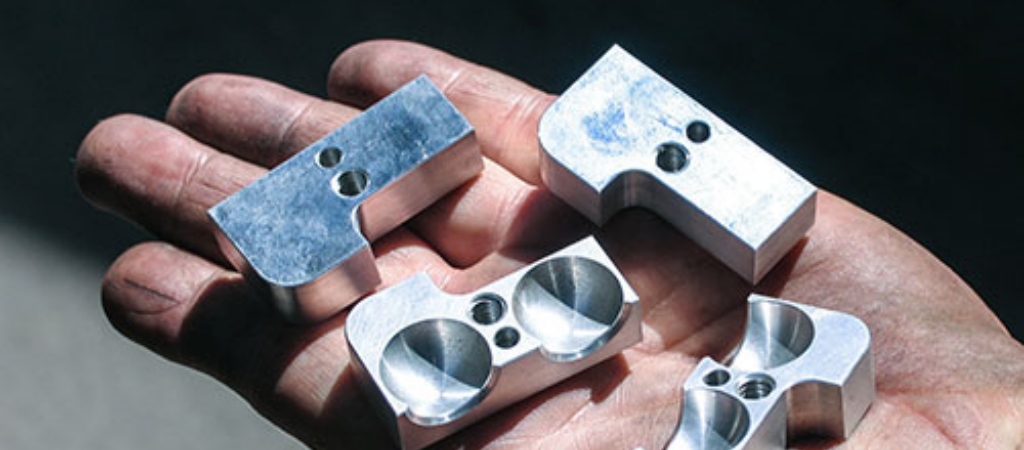
When it comes to designing machined parts, it's crucial to pay attention to the smallest details. Overlooking certain aspects can lead to prolonged machining time and costly iterations. In this article, we highlight five common errors that are often underestimated but can greatly improve design, reduce machining time, and potentially lower manufacturing costs.
1. Avoid Unnecessary Machining Features:
One common mistake is designing parts that require unnecessary machining operations. These extra processes increase machining time, a critical driver of production costs. For example, consider a design that specifies a central circular feature with a surrounding hole (as shown in the left image below). This design necessitates additional machining to remove excess material. Alternatively, a simpler design (shown in the right image below) eliminates the need for machining the surrounding material, significantly reducing machining time. Keeping designs simple can help avoid unnecessary operations and reduce costs.
2. Minimize Small or Raised Text:
Adding text, such as part numbers, descriptions, or company logos, to your parts may seem appealing. However, including small or raised text can increase costs. Cutting small text requires slower speeds using very small end mills, which prolongs machining time and raises the final cost. Whenever possible, opt for larger text that can be milled more quickly, reducing costs. Additionally, choose recessed text instead of raised text, as raised text requires machining away material to create the desired letters or numbers.
3. Avoid High and Thin Walls:
Designing parts with high walls can present challenges. Tools used in CNC machines are made of hard materials like carbide or high-speed steel. However, these tools and the material they cut can experience slight deflection or bending under machining forces. This may result in undesirable surface waviness, difficulty in meeting part tolerances, and potential wall cracking, bending, or warping. To address this, a good rule of thumb for wall design is to maintain a width-to-height ratio of approximately 3:1. Adding draft angles of 1°, 2°, or 3° to the walls gradually tapers them, making machining easier and leaving less residual material.
4. Minimize Unnecessary Small Pockets:
Some parts include square corners or small internal pockets to reduce weight or accommodate other components. However, internal 90° corners and small pockets can be too small for our large cutting tools. Machining these features may require the use of six to eight different tools, increasing machining time and costs. To avoid this, reassess the significance of the pockets. If they are solely for weight reduction, reconsider the design to avoid paying for machine material that doesn't require cutting. The larger the radii on the corners of your design, the larger the cutting tool used during machining, resulting in shorter machining time.
5. Reconsider Design for Final Manufacturing:
Often, parts undergo machining as a prototype before being mass-produced through injection molding. However, different manufacturing processes have distinct design requirements, leading to varied outcomes. Thick machining features, for example, may cause sinking, warping, porosity, or other issues during molding. It's important to optimize the design of parts based on the intended manufacturing process. At Hyluo CNC, our team of experienced process engineers can assist you in modifying your design for machining or prototyping the parts before final production through injection molding.
Sending your drawings to Hyluo CNC's machining specialists guarantees a speedy review, DFM analysis, and allocation of your parts for processing. Throughout this process, our engineers have identified recurring issues in drawings that extend machining time and lead to repeated sampling.
For additional help, feel free to contact one of our applications engineers at 86 1478 0447 891 or hyluocnc@gmail.com.